How Welding Inspection Madison Ensures Quality and Safety in Fabrication
How Welding Inspection Madison Ensures Quality and Safety in Fabrication
Blog Article
The Significance of Thorough Welding Evaluation in Industrial Applications
In the realm of commercial applications, the value of precise welding assessment can not be overemphasized. As we explore the multifaceted benefits of thorough welding examinations, one must think about the wider effects on safety and security, reliability, and cost-effectiveness in industrial operations.
Enhancing Structural Stability
When it involves welding examination in commercial applications, enhancing structural integrity is critical. The main objective of welding assessment is to make certain that the welds can bearing the anticipated stress and anxieties and lots they will certainly run into in solution. This entails a thorough evaluation of the welds' dimensions, alignment, and overall top quality, guaranteeing they fulfill the defined requirements and codes. Accurate evaluation methods, such as visual inspection, ultrasonic screening, and radiographic screening, are vital in determining problems that could compromise the framework's security and performance - Welding Inspection Madison.
The significance of keeping architectural honesty in bonded structures can not be overemphasized. Badly implemented welds can cause catastrophic failures, leading to costly fixings, downtime, and even endangerment of human lives. Inspectors play a crucial function in the lifecycle of industrial parts, giving assurance that the welding procedure provides the wanted stamina and resilience.
Additionally, advanced technologies, such as phased range ultrasonic testing and digital radiography, deal improved abilities in spotting possible weak points, enabling restorative measures prior to problems rise. By focusing on the stability of welds with precise examination, markets can ensure functional performance and prolong the longevity of their infrastructure.
Determining Welding Problems
Determining welding flaws is a crucial element of guaranteeing the security and integrity of welded structures. These flaws can compromise the integrity of the entire assembly and, if left unaddressed, might bring about devastating failings. Common welding issues include porosity, splits, incomplete fusion, and damaging. Each of these issues arises from certain causes, such as incorrect welding strategies, contamination, or poor warm control.
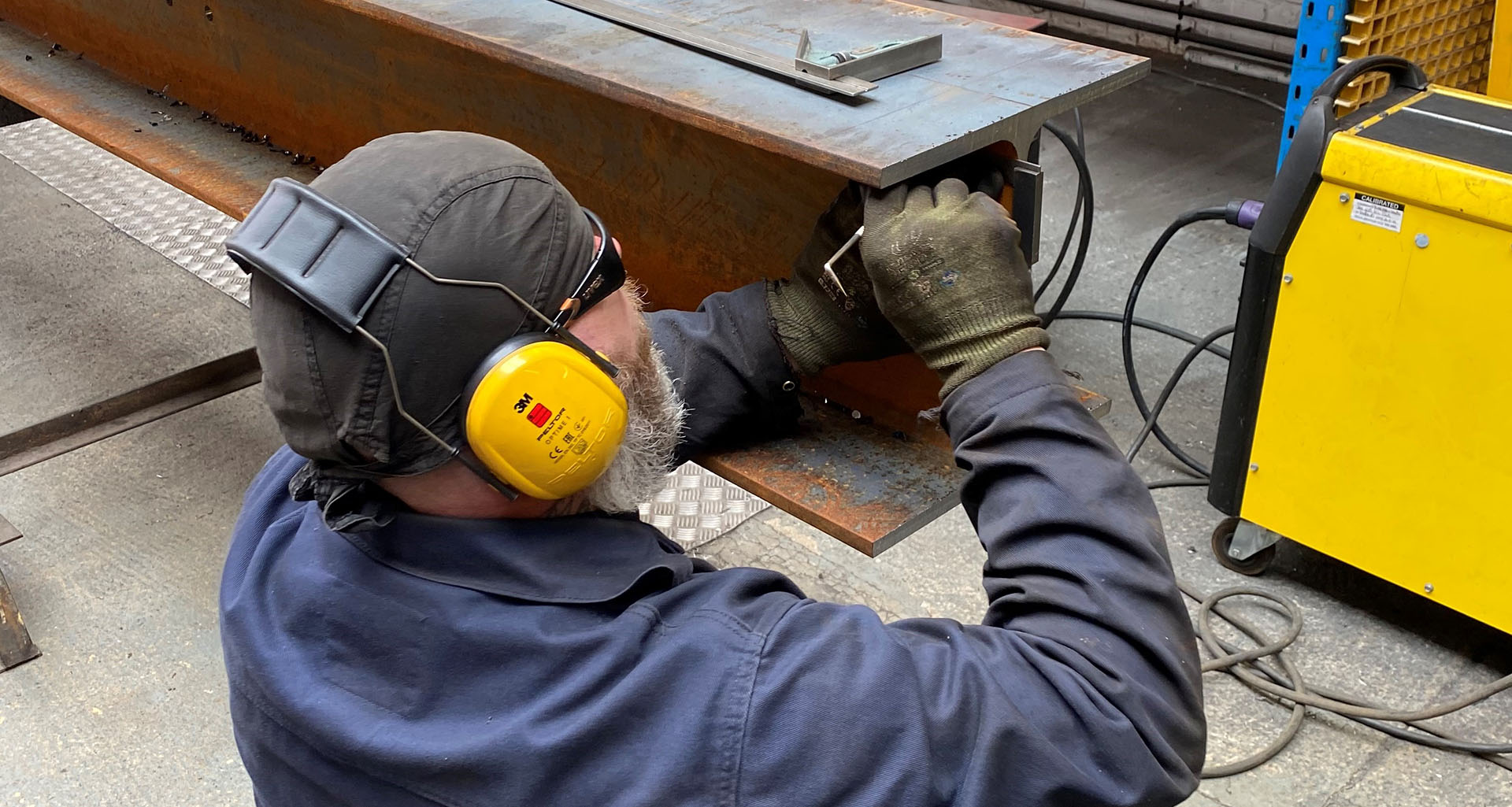
Experienced examiners make use of both aesthetic evaluation and progressed non-destructive testing (NDT) methods, such as ultrasonic or radiographic testing, to detect these issues. The timely recognition and rectification of welding issues are critical to keep the architectural integrity and durability of commercial elements.
Making Sure Compliance Standards
Compliance with established criteria, such as those given by the American Welding Society (AWS) and the International Company for Standardization (ISO), makes sure that welds satisfy minimum safety and security and top quality demands. These standards encompass a vast variety of criteria, consisting of product specifications, welding procedures, and credentials of welders.
Regular audits and examinations are necessary in verifying conformity. Inspectors need to possess a thorough understanding of the relevant requirements and be adept at making use of various non-destructive screening (NDT) approaches to review weld high quality. By ensuring that welding methods straighten with compliance requirements, companies reduce the risk of non-conformity, which can lead to lawful obligations and security browse around this site hazards.
In addition, preserving compliance not just safeguards architectural honesty but likewise improves a firm's reputation in the market. Customers and stakeholders are more probable to trust fund companies that consistently demonstrate a dedication to top quality and safety and security through extensive conformity. Therefore, making certain compliance standards is an important part in the effective execution of welding in industrial applications.
Reducing Maintenance Costs
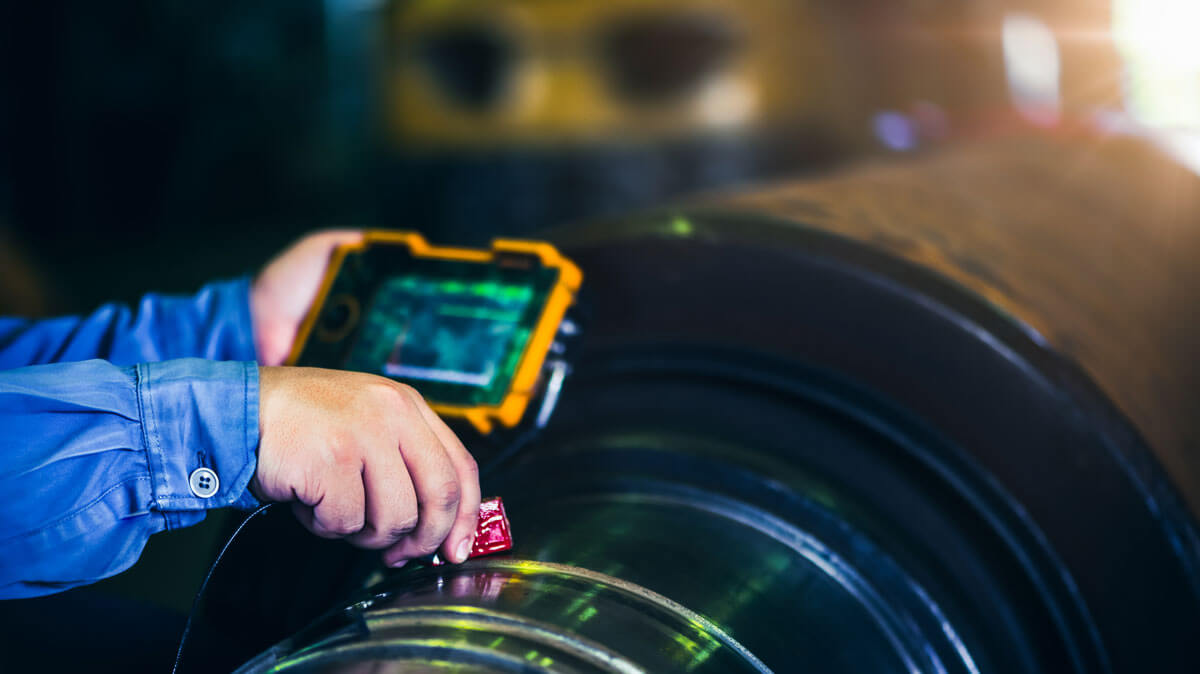
The application of innovative non-destructive screening (NDT) methods, consisting of ultrasonic, radiographic, and magnetic particle examinations, improves the capacity to find subsurface defects without endangering the structural honesty of elements. By using these techniques, sectors can considerably expand the service life of their tools, decreasing downtime and the linked financial worry of maintenance activities.
In addition, a robust welding examination regime sustains the optimization of upkeep schedules, moving from responsive to predictive maintenance approaches. This proactive method not only stops unforeseen failings yet also enhances source allotment, making sure that upkeep efforts are focused and efficient. Inevitably, the investment in rigorous welding assessment is countered by the significant savings recognized with lowered upkeep needs, contributing positively to the overall operational effectiveness of commercial ventures.
Improving Precaution
Welding assessment plays a vital role in this context, as it ensures that all links and joints satisfy stringent safety and security standards. Comprehensive evaluations help determine issues such as fractures, porosity, or incomplete blend that might compromise architectural stability.
Methods like ultrasonic screening, radiographic screening, and magnetic particle evaluation enable for thorough examination without damaging the structure. Applying a durable quality control system that includes routine training for view it now examiners and welders ensures adherence to established safety requirements.
Finally, cultivating a society of safety and security within the organization emphasizes the significance of complete welding examinations. Encouraging open communication and collaboration among engineers, inspectors, and welders adds to a common dedication to safety and security quality. Welding Inspection Madison. In doing so, sectors can secure their procedures, secure workers, and preserve public count on

Conclusion
Detailed welding assessment is indispensable in commercial applications, significantly improving architectural integrity and dependability. Ultimately, the thorough implementation of welding evaluations plays a vital role in preserving functional efficiency and security in commercial setups.
As we explore the diverse advantages of diligent welding assessments, one need to take into consideration the broader ramifications on security, reliability, and cost-effectiveness anonymous in industrial procedures.
The key goal of welding evaluation is to make sure that the welds are qualified of bearing the expected tons and anxieties they will experience in solution. Reliable welding examination plays an integral role in reducing these expenses by making sure the honesty and long life of welds, therefore mitigating the risk of early failings.Comprehensive welding evaluation is important in industrial applications, substantially improving structural stability and reliability. Inevitably, the diligent implementation of welding examinations plays a critical duty in keeping functional effectiveness and security in industrial setups.
Report this page